Ross Harrison Q&A: 'Engage suppliers early in the design and engineering process'
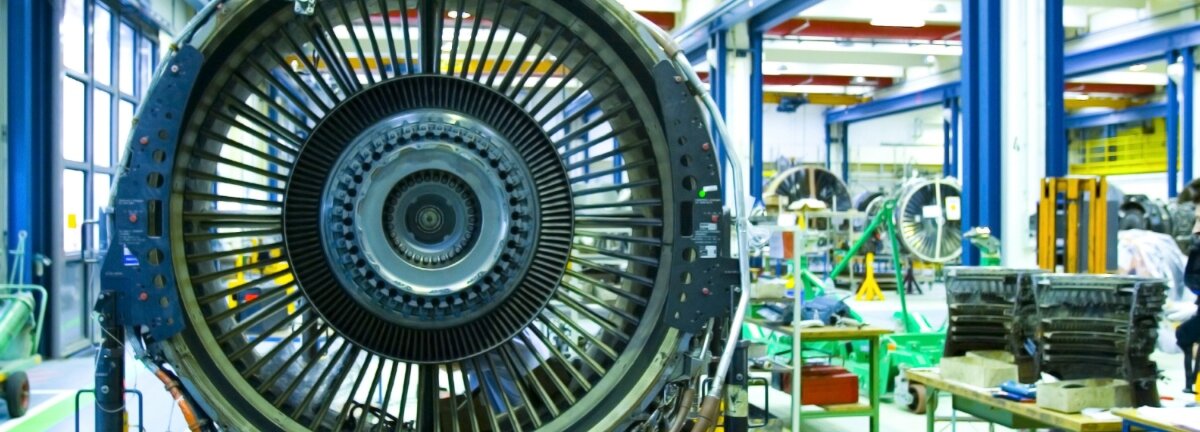
Our new research conducted for the Leading Business by Design Summit explores the impact design has on the manufacturing sector, and takes an in-depth look at how it could positively affect supply chains. We spoke to Ross Harrison, Supplier Development Engineer at Controls and Data Services, about some of the supply chain issues he faces and how design could be a solution.
Tickets are still available for 18 June’s Leading Business by Design Summit - follow this link and enter promotional code ‘GOAT200’ to receive £200 off your ticket.
Could you explain what it is you do, Ross?
I’ve worked as a supplier development engineer in the aerospace and defence industries for almost 10 years. In my role, I work closely with suppliers and am privileged to see first-hand the issues they face and problems we as a customer cause them on a day-to-day basis.
What’s the most common gripe that you get from suppliers that you work with?
One of the main frustrations I hear time and time again is: “If we’d have been involved earlier we wouldn’t have this problem.”Suppliers are typically more than happy - if not eager - to be involved in the design phases of a new project. It is in their interest to be engaged and as specialists in their field they can typically add real value to the design process.
Do suppliers get involved, in practice?
I have seen a handful of examples where suppliers have been engaged early in the design phase for their expertise and knowledge of special materials or processes and can wholeheartedly say it has never had a negative repercussion - sadly however, it is the exception rather than the norm.
What’s the strongest argument for having design involved as early as possible?
As I’m sure you will be aware, retrospective engineering change is costly and often a very difficult thing to achieve, particularly when a product is in production. As a result of this, many potential improvements to a product such as design for manufacture considerations, cost reductions, quality issues and so on have to be ignored as it is simply too late to make the change. This makes the job of people like myself looking to make improvements and reduce the cost of parts and processes that much more difficult.
So, is there a straightforward answer?
What I believe we need to recognise is while we may be the design authority and manufacturer of the products we bring to market, we are unlikely to be the specialist in all the intricate details and component parts that make up our final assemblies. The primary reason we subcontract work to our suppliers is that the product or process in question is not something we consider a core competency of our business. Why, therefore, would its design be any different?
What new technology do you think will have the most impact on manufacturing in the next ten years?
There are some exciting growth and emerging technologies I have had some visibility of. From the point of view of design, 3D printing has to be at the top of the list because of the capability it offers to manufacture forms that have been previously impossible to produce. From my point of view as a lean manufacturing specialist, I believe there is a lot more we can do to harness the capability of computers to control processes; for data acquisition, for communication and to slicken the interface between man and machine.
Do you think there’s a skills shortage in British manufacturing?
I’m certain there is a skills shortage in British manufacturing. The focus of undergraduate education seems to have - for some time - been on the service and financial sectors with a perception that engineering and manufacturing are in decline. Thankfully, the UK retains a core of high complexity and high value manufacturing businesses and we are still considered a world leader in the engineering world. This is, however, becoming an increasingly competitive marketplace and without continuous improvement and innovation, our standing will continue to be eroded by the significant improvements of developing nations.
Do you think that design should be in the makeup of more manufacturers’ skills?
Design is certainly fundamental to the industry. I believe design expertise, whilst not critical in all parts of the supply chain, would undoubtedly serve to support customers in the design phases of new projects and increase collaborative working between customer and supplier. This would clearly help lower tier suppliers move up the value chain and should help to increase the specialist knowledge available in the industries skill base overall. This is, however, reliant on us as customers facilitating these good working practices and making use of design support from our supply chains.
The Leading Business by Design Summit is quite a different event for this sector, what do you expect to learn there?
I’ve always considered best practice sharing and networking as a key part of my role. The Summit promises to be an ideal opportunity to learn from the experiences of others and crucially get a feel for how a broad range of other industry sectors are addressing similar problems.
Get £200 off your Leading Business by Design Summit ticket - follow this link and enter promotional code ‘GOAT200’.
Subscribe to our newsletter
Want to keep up with the latest from the Design Council?